- HOME
- Solution
- Energy Saving Air Conditioning System RiCS
- Customer Feedback
Customer Feedback
Customer Feedback
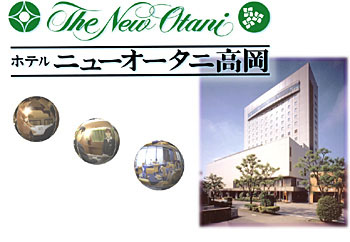
This system is very flexible because the screen can be changed easily. We are also satisfied with prompt responses to complaints and requests.
Hotel New Otani Takaoka
Person in charge of building management
Episode after Introduction of the System
1. User friendliness
- For a hotel:
- The RiCS that has been used in the hotel malfunctioned.
We explained to the 80-year-old landlady that the system can be operated in manual mode, but she could not operate the equipment without RiCS. We dispatched an engineer to the hotel to repair RiCS.
- For a training facility:
- We had a request to add a button to start and stop the equipment by batch based on the schedule.
We added the desired button and functions according to their request. They were very pleased with the function.
- For a public bath facility:
- We had a request to modify the system so that only the specified person can conduct the scheduled operation of the equipment.
The client was pleased with the new function because the equipment had been operated by many unspecified people and had not been properly controlled before.
- For a medical facility:
- It was necessary to reset the exhaust fan in the machine room after a power failure. However, staff sometimes forgot to reset it.
We added the function of an alarm message being given if the exhaust fan is not operating after a power failure. The client is pleased with this function because it reminds the operators to reset the exhaust fan.
2. Flexibility
- For a city hotel:
- After guests had checked out, cleaning staff had to reset the air conditioner in each room. This was time-consuming.
We added a function to the air conditioning system that enabled the air conditioners of all rooms to be reset simultaneously, without the need for remote control switches.
The client was very pleased with this function.
- For a sports facility:
- The control unit of the air conditioner installed outside of the facility has an inverter in which the frequency can be changed according to the status of the facility.
In order to save energy, we installed CO2 sensors to detect the temperature, and created a program at the site.
- For renovation of an existing system:
There was a demand control function in the system. However, a demand signal could not be obtained because the watt-hour meter had been changed. It was difficult to replace the demand signal unit due to high cost.
In order to use the demand control function, we developed a special software for a local system that receives 4-20mA of power. We calculated the demand signals to predict the demand for power consumption.
- For a newly built hospital:
- Because of a budget problem, they could not receive demand signals from the watt-hour meter installed at the electric pole away from the hospital building.
The client was dissatisfied with the existing system because they wanted to control power demand.
There were no demand signals, but since pulse signals were received from the electric equipment, we were able to add a demand control function using those signals.
- For a medical facility:
- When we installed an air conditioner in the server room, they were worried about the temperature in the room because it could be changed easily by means of the remote-control switch.
We installed a sensor that emits an alarm when the air conditioner’s operation mode is changed to a mode other than the cooling mode. In addition, we modified the system so that an alarm is emitted when the temperature is lower than the specified temperature.
3. Promptness
- For a medical facility:
- A client who was using another company’s central monitoring system found it difficult to identify the cause when a malfunction occurred — whether it was in the central control system, the control circuit or the equipment itself. It could take several days and even a few weeks to identify the cause and solve the problem.
We modified the system and quickly solved the problem by means of our RiCS. Our one-stop solution enabled us to restore the system within a day. The client was satisfied with our modification.
- For a hotel:
- The client was using NEC PC98 as the interface for the system. The maintenance period for the PC98 series had expired when it malfunctioned. They asked us to repair it as soon as possible.
Normally it takes about two months to prepare the unit and create software. We developed software that operates with minimal functions and completed the system for the equipment in three days.
- For an office building:
- They asked us to integrate the measured value of the gas meter into the central monitoring screen and to indicate the location of the meter on the plan view.
We created an illustration of the gas meter for the monitor screen. The client was very pleased with our response to their request.